Quiz on Flow Valves
![]() | ![]() | ![]() | ![]() | ![]() |
---|
1. A fail-open valve is the same as a(n):
- Incorrect. Air pressure opens the valve. The absence of air pressure closes the valve.
- Correct. Air pressure closes the valve. The absence of this air pressure opens the valve.
- Incorrect. When the valve fails, pressure is released and closes the valve.
- Incorrect. A globe valve may be designed to be either fail-open or fail-close
2. Why is it desirable to maintain a linear relationship between valve lift and flow rate? Select three correct answers without selecting the one that is incorrect.
- Incorrect. Linearity does not affect valve stem travel. If there is excessive valve movement then it can wear out the components such as the seals or motor
- Correct. Nonlinear relationship between lift and flow means that the valve changes will either cause large or small changes in flow depending on whether the valve is mostly opened or closed.
- Correct. Nonlinear relationship between lift and flow means that the valve changes will either cause large or small changes in flow depending on whether the valve is mostly opened or closed.
- Correct. A linear relationship means that one PID controller gain `K_c` will be tuned correctly over the entire range of operation for the flow controller. Recall that IMC tuning with no dead-time recommends `K_c = 1/K_p`. If the lift to flow is linear then the process gain `K_p` is the same throughout the range of operation such as 5% open or 95% open.
3. What is one way to create a linear relationship between valve lift and flow rate?
- Incorrect. PID gain scheduling is a method to compensate for a nonlinear relationship by changing the controller gain `K_c` based on the PV measurement. This extra complication for a flow controller can be avoided by selecting a valve trim that creates a linear relationship between lift and flow.
- Incorrect. This does affect the relationship between lift and flow but only as a scalar. It changes the slope of lift versus flow but does not correct for nonlinearity.
- Correct. The valve trim can be changed to another shape to create a linear relationship between lift and flow. The process pressure drop is often a quadratic function of flow. The equal percentage valve trim is commonly used to compensate for this nonlinear (quadratic) relationship.
- Incorrect. `\Delta P_v` is not a design variable. It depends on the valve lift, flow, and valve design.
4. Pump pressure is dissipated across the system and valve that maintains the flow rate through the system.
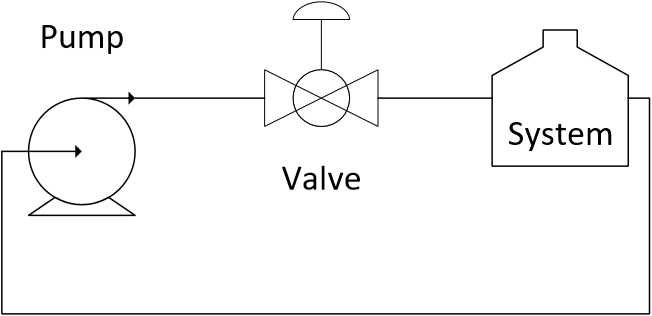
$$\Delta P_{pump} = \Delta P_{valve} + \Delta P_{system}$$
The pump generates `\Delta P_{pump}` with 50 bar of pressure. The pressure drop across the system (not including the valve) has a quadratic relationship with flow `\Delta P_{system} = 2 q^2` bar where `q` has units of `m^3/{hr}`. If the flow through the valve and system is `q = 4.4` `m^3/{hr}`, what is the pressure drop across the valve `\Delta P_{valve}`?
- Incorrect. This is the system pressure drop, not the pressure drop across the valve.
- Incorrect. This is the correct range for the valve pressure drop, between 1/4 and 1/3 of the total pressure drop. If the fractional pressure drop is too high then the `C_v` should be increased with a larger valve.
- Correct. `\DeltaP_{valve} = \DeltaP_{pump} - \DeltaP_{system} = 50 - 2 (4.4)^2 = 11.28` bar
- Incorrect. This is the correct range for the valve pressure drop, between 1/4 and 1/3 of the total pressure drop. If the fractional pressure drop is too high then the `C_v` should be increased with a larger valve.