Cascade Control
![]() | ![]() | ![]() | ![]() | ![]() | ![]() |
---|
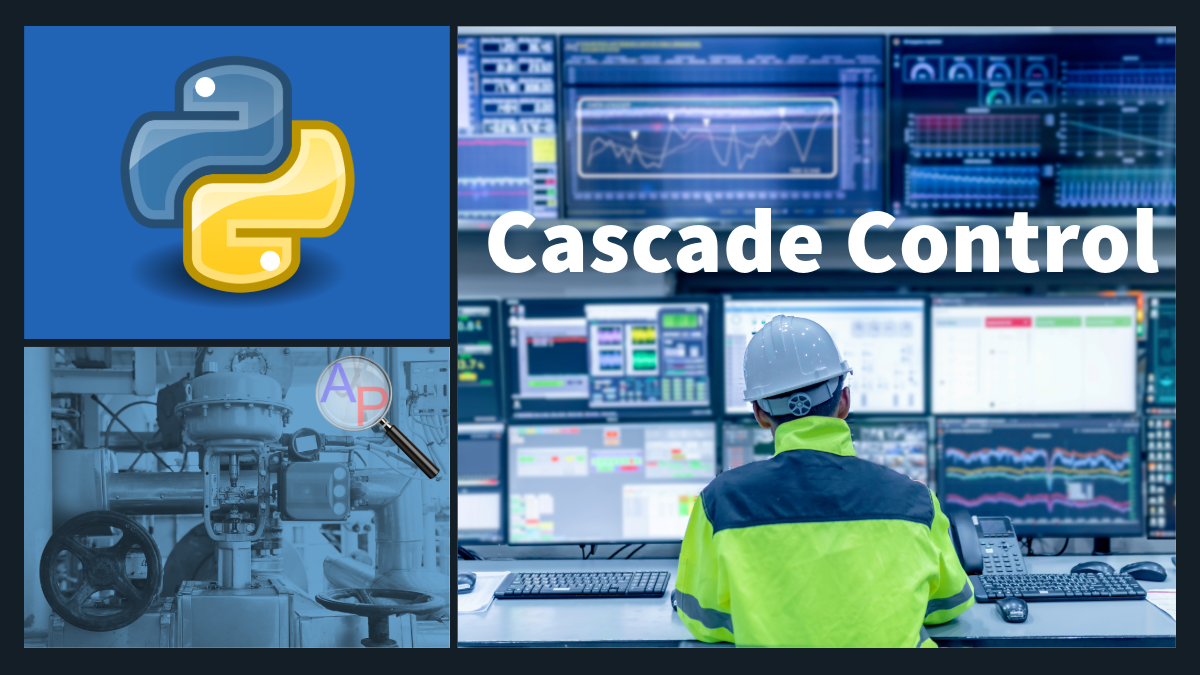
Cascade control is a strategy in process control that uses a hierarchy of control loops. Typically, a primary (outer) loop controls the process variable of interest, while a secondary (inner) loop controls a faster-responding auxiliary variable that directly affects the final control element (FCE). In cascade control, the primary controller sends its setpoint to the secondary controller, which fine-tunes control actions to mitigate disturbances quickly. This two-layered control structure allows for more robust disturbance rejection compared to a single-loop system, especially for processes with significant time delays or complex dynamics.
When to Use Cascade Control
Cascade control is beneficial in situations where:
- Disturbances affect a process variable that influences the final control element. If an upstream variable can be controlled to prevent the disturbance from reaching the primary process variable, a secondary loop can help isolate the disturbance effects.
- Secondary variables respond more quickly than the primary process variable. For example, in a temperature control loop with a heated liquid, flow rate changes can quickly adjust the temperature, so a secondary flow control loop can help maintain stable temperature control.
- Precision is required for critical processes. In applications where precise control is crucial, the cascade arrangement ensures faster and more stable responses to process changes or disturbances.
Industrial Examples of Cascade Control
- Temperature Control in Heat Exchangers A common application of cascade control is temperature regulation in heat exchangers. The primary loop controls the outlet temperature by adjusting the setpoint of a secondary loop that regulates steam or cooling water flow. This setup quickly mitigates changes in flow rate or steam pressure, keeping the temperature within desired limits.
- Level Control in a Tank with a Flow Control Loop In tank level control, the primary loop maintains the tank level, while the secondary loop controls the inflow rate. This arrangement is helpful when large changes in inflow or outflow could disturb the tank level. The secondary loop responds immediately to flow changes, keeping the level steady.
- Pressure Control in Compressors Cascade control is also used in compressor control systems, where the primary loop might maintain a desired pressure, and the secondary loop controls compressor speed. By regulating speed, the system can respond to load changes more quickly, maintaining stable pressure even with fluctuating demand.
Feedforward vs. Cascade Control
Feedforward control anticipates and compensates for disturbances by measuring them before they affect the primary variable. Unlike cascade control, feedforward control does not require a secondary measurement to close a feedback loop. It adjusts the manipulated variable based on disturbance predictions, making it suitable when disturbances can be accurately measured and predicted.
Cascade | Feedforward | |
---|---|---|
Sensors | 2 | 2 |
Controllers | 2 | 1 |
Valve | 1 | 1 |
Model | 0 | 1 |
Restrictions | settling time small for inner loop |
θp < θd |
- When to use feedforward control: Use feedforward control when disturbances can be accurately measured before affecting the process. This approach is highly effective if the disturbance magnitude and effect on the controlled variable are well understood.
- When to use cascade control: Use cascade control when disturbances are best managed locally, and a fast-response variable (measurable before it affects the main process variable) can provide better disturbance rejection through an additional loop.
Example Comparisons of Cascade and Feedforward Control in Chemical Processes
- Disturbance Rejection in a Reactor Temperature Control
In a chemical reactor, the temperature might be controlled using cascade control with an inner loop for steam flow rate and an outer loop for reactor temperature. Here, cascade control quickly addresses changes in steam pressure or flow variations before they impact the reactor temperature. Alternatively, if the feed composition changes can be accurately measured before entering the reactor, feedforward control can adjust the steam flow preemptively. Feedforward control, however, would be less effective for unmeasured or rapid disturbances.
- Distillation Column Control
Distillation columns often use cascade control for feed rate or reflux ratio adjustments. A primary loop might control the composition, while a secondary loop handles flow rates, responding faster to changes in feed quality. This cascade setup allows quick adaptation to flow or feed disturbances. In contrast, feedforward control is used if a measurable disturbance (like a change in feed temperature) can be preemptively corrected by adjusting the reflux ratio before it affects the column composition.
Assignment